
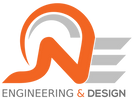

Short Run Manufacturing
Whether you need a hundred parts every few months; or you need hundreds of thousands of parts every month, our short run manufacturing service is for you. It’s great if you need small quantities on a regular basis or if you want to bridge the gap between the prototyping stage and full-scale production. Get to market faster with JNE Engineering short run manufacturing service.
Our team work with you every step of the way, from initial design review and quotation to inspection and delivery, so contact our friendly team to get a free quote for your next project.
​
Benefits Of Short Run Manufacturing
​
Many of our customers choose short run production to allow for flexibility in customization and design changes, to test the market, and for cost savings. This is especially true if we have already worked with them on creating the initial prototype of a new design idea. With our fast, short run process, you can have your parts quickly. When you need more we will have your tool on hand ready to go. This will ensure you save time every time.

Plastic Injection Molding
At JNE Engineering, we specialize in high quality custom plastic injection molding and mold tool making. Plastic injection molding is by far the industry’s most common way to manufacture parts, especially when making larger quantities. We provide custom molding for 50 to 100,000+ parts as well as a wide range of other manufacturing and finishing services to complete your project.
​
Plastic injection molding involves melting granular plastic pellets into a liquid form and then compressing this liquid into the empty cavity of a mold tool. The plastic will retain the shape of the mold as well as the surface texture of the walls of the cavity. After an optimized injection and cooling phase, the now solidified plastic part is ejected and the molding cycle is repeated. This molding cycle can take from as little as a few seconds to several minutes depending upon part size, molding resin and part design.
​
Mold Tooling Production
​
Materials such as aluminum 7075, pre-hardened tool steel such as P20 and fully hardened tool steels like H13 are most commonly used when making your mold tool. The material used will depend on the number of parts you wish to produce.
​
​
Aluminum Tooling
​
Aluminum tools are quickest to produce and most cost effective. Aluminum is softer and therefore suited to smaller volumes. For larger volume production, and for aggressive resins or part geometries requiring thin blades or ribs it’s best to use harder materials that are more durable.
Steel Tooling
​
Steel tools are tougher and more durable but can take longer to produce. These are suited for larger volumes or when injecting abrasive or corrosive plastics that would damage aluminum molds. Pre-hardened tool steel is used for quantities of 100K pcs and more, depending on plastic material and part geometry. We use P20 and NAK80 stress-relieved steel. Fully-hardened tool steel is the most durable and can be used for millions of injected parts. H13 hardened steel is ideal for full production volumes or when injecting abrasive engineering-grade plastics.